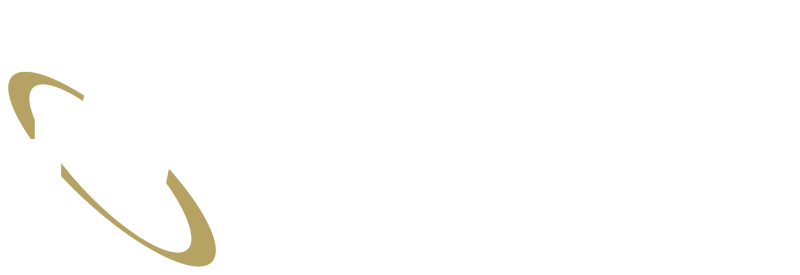
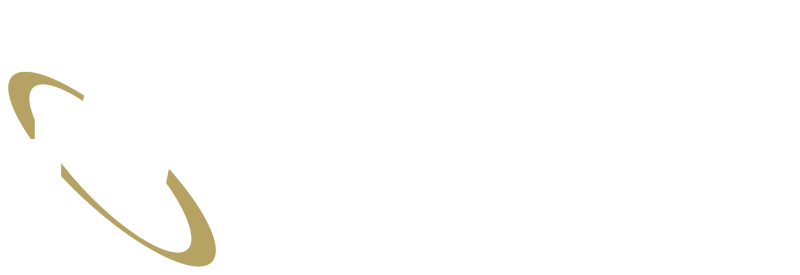
Tira aria di crisi in casa Toyota. Fino a qualche tempo fa il suo sistema di produzione era un vanto, lodato da più parti. Una serie di gravi disfunzioni e inconvenienti, intervenuti nel recente periodo, ha messo in dubbio il mito dell’efficienza della lean production e la fiducia dei consumatori.
Nel giro di un anno Toyota ha dovuto richiamare oltre 10 milioni di vetture per problemi tecnici, causando un danno enorme alla propria immagine e alla propria affidabilità.
In ottobre, il gigante giapponese, quinto nella classifica Global Fortune 500, ha dovuto chiedere alla clientela di riportare indietro 1,5 milioni di automobili Lexus, il marchio di lusso, sulle quali è previsto un intervento di sostituzione del connettore della pompa di benzina e della guarnizione della pompa dei freni.
In base a recenti stime risulta che la produzione della multinazionale del Sol levante, il cui primato mondiale è stato scippato da Volkswagen, è calata del 16% in Usa ed in Europa del 30%.
Secondo Jeffrey K. Liker, uno dei massimi conoscitori del “toyotismo”, docente alla University of Michigan di Industrial and Operations Engineering ed autore del famigerato testo “The Toyota Way”, sarebbe azzardato parlare di fallimento perché nei casi più gravi non ci troveremmo davanti ad una defaillance del manufacturing, ma ad errori di natura differente ad opera di un dealer.
Tuttavia, malgrado la difesa dei suoi portabandiera, Toyota resta nel mirino della critica. Eppure il TPS (Toyota production system), considerato un sostituto o un’evoluzione del modello della produzione di massa taylorista e fordista, si è imposto sul piano internazionale grazie all’introduzione di una nuova filosofia produttiva, la cui paternità va riconosciuta a Taiichi Ohno, che ha consentito di regolare meglio il processo lavorativo in rapporto al mercato. Tra i suoi fondamentali obiettivi, il recupero della produttività mediante riduzione al minimo, o eliminazione, dell’inefficienza nel sistema organizzativo aziendale, degli sprechi nella gestione delle risorse e dei “tempi morti” nel funzionamento dell’organismo aziendale guidato dall’imperativo kaizen (miglioramento continuo).
Verso la fine degli anni ’80 alcuni studiosi del MIT Womack, Jones e Roos, coniarono il termine “produzione snella” (lean production) con riferimento al TPS.
Alla sua base sono posti due pilastri: il just in time e l’autoattivazione. JIT significa riduzione dei costi globali e parallelamente compressione del lead time di consegna al cliente con l’ambizione di superare i limiti dello stoccaggio per rendere possibile un flusso produttivo continuo. Autoattivazione o autonomazione, invece, capacità dell’apparato produttivo o della “macchina”, di “retroagire con l’ambiente”, in particolare con la forza-lavoro, cui si consente di intervenire in tempo reale per correggere il difetto di produzione. Questo meccanismo tende a realizzare «prodotti in serie brevi e differenziate con aggiustamenti continui alle fluttuazioni della domanda che tira la produzione (sistema pull)», (Giuseppe Bonazzi).
Il toyotismo implica per poter funzionare, oltre la diminuzione degli sprechi e il coinvolgimento dei dipendenti nelle decisioni relative alla produzione, altri fondamentali requisiti come la partecipazione dei fornitori e la ricerca della Qualità Totale.
Ma un ulteriore importante elemento, sottolineato da Shigeo Shingo, ingegnere collega di Ohno, noto per aver contribuito all’elaborazione del TPS, è rappresentato dal retroterra culturale dell’impresa giapponese (management e maestranze compresi), incardinata sui valori di lealtà e fedeltà assoluta nonché sul concetto di “vita di gruppo” che porta ad esasperare i tratti di appartenenza identitaria fino a livelli parossisitici difficilmente accettabili e trapiantabili in altre società.